RNG Facility
Landfill Gas to become Renewable Natural Gas Fuel
On October 21, 2022, Will County cut the ribbon on a brand new 20,000-square-foot RNG facility at the Prairie View Landfill in Wilmington. The plant sits on a 1.5-acre site making use of the same pipes that carried the gas generated by the landfilled waste to the former gas-to-electricity generators and the landfill flares for excess methane to be burned off per US EPA regulations. The County decided to expand efforts to recover the gas and determined the most benefical effort was to build a state-of-the-art system to repurpose methane gas into transportation fuel as a replacement for fossil fuels, such as diesel.
The RNG Plant upgrades the landfill gas into pipeline-quality gas, transferring it into
renewable, revenue-generating transportation fuel. Will County continues to be on the cutting edge of sustainability and renewable energy – This plant was only the second in Illinois
to operate and the first in the Chicagoland region.
• Landfills produce a variety of gases, including methane. Currently, these gases are often burned in the flare into the atmosphere.
• The new RNG Plant utilizes all the available landfill gas and upgrade it into pipeline-quality renewable natural gas.
• After cleaning and upgrading the methane gas, it is transferred externally to an interstate pipeline.
• The gas will be utilized as transportation fuel for energy-efficient vehicles for the equivalent of nearly 150 million miles traveled annually.
• Environmental:
Capturing and repurposing methane, a potent greenhouse gas generated by landfilled waste.
Compared to an equivalent amount of gasoline, utilizing this RNG for transportation will reduce greenhouse gas emissions by more than 50 percent.
• Financial:
A self-sustaining project, the plant is projected to raise millions of dollars annually for the Will County Budget.
The renewable natural gas produced will raise revenue for the county through both commodity sales and credits paid by fossil fuel providers.
FAST FACTS
• First Landfill Gas-to-Fuel Project in Northern Illinois, second in the State
• 96% of project work was performed by local companies
• 44% of project work was performed by Will County residents
• 50% of landfill gas is methane
• Natural gas is 70% to 90% methane
• The plant will recover a minimum of 93% of methane
• Construction began on June 2021 and ended October 2022
How it Works!
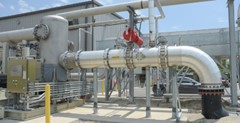
Initial Pressurization (Multistage Centrifugal Blower)
Biogas is extracted from the landfill gas collection and control system (GCCS) by a centrifugal blower system which places a vacuum on the landfill GCCS, which pulls the biogas from the landfill. The blower system then pressurizes the biogas so that it enters the facility for processing.
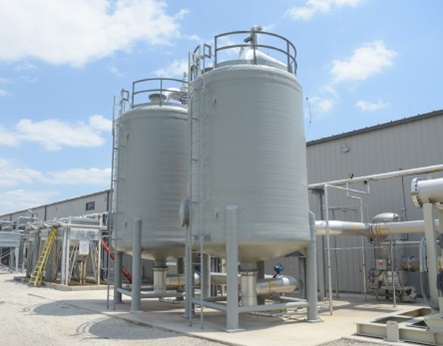
Hydrogen Sulfide (H2S) Removal (Norit Carbon Media)
Hydrogen sulfide (H2S) is a toxic, flammable, and corrosive gas with a rotten egg smell that can be a common impurity in biogas. It can damage pipes, valves, and can impact the performance of gas upgrading units. Before biogas can be sold as Renewable Natural Gas (RNG) to a commercial pipeline, it must be treated for H2S contamination.
Activated carbon is a common method for removing hydrogen sulfide from biogas during the advanced treatment stage purification. This process involves treating the biogas with activated carbon, which is typically associated with adsorption, a physical process where dissolved molecules stick to the carbon filter’s surface.
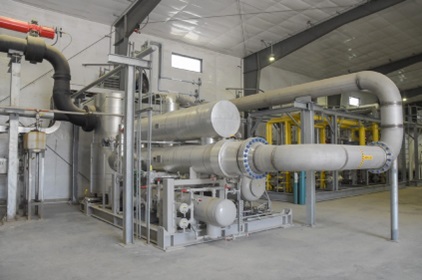
Biogas Chilling / Dehydration (Vilter Biogas Chiller)
Gas (Biogas) coming into the facility from the adjacent landfill is chilled during the process to upgrade the biogas by removing residual moisture to meet natural gas pipeline specifications. It is crucial that this moisture is removed from the biogas prior to further processing, as water vapor from gas streams can damage downstream equipment and cause corrosion in pipelines.
The separation process cools biogas to low temperatures (40 degrees Fahrenheit), causing
moisture and other components to separate from the biogas. This process helps to eliminate moisture, that can corrode equipment or affect the quality of the product gas, Renewable Natural Gas (RNG).
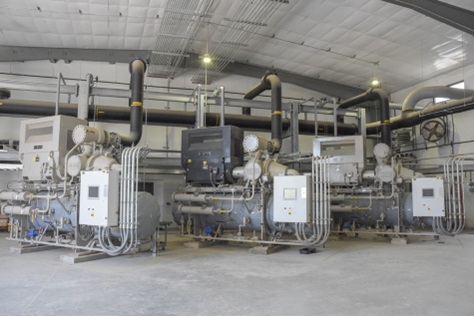
Feed Compressor (Vilter VSG Single Screw Compressor)
A single screw compressor is used for its reliability and energy efficient characteristics. Each compressor has a 1250 horsepower electric motor powering the unit to compress biogas. Compressed Biogas (200 pounds per square inch) is routed through a system of pipes to the next step, the carbon dioxide processing portion of the biogas purification process.
Associated piping networks circulate compressor oil to an oil cooler outside to release heat from the oil that is created during the compression process. The cooled oil is then returned to lubricate and cool the compressor.
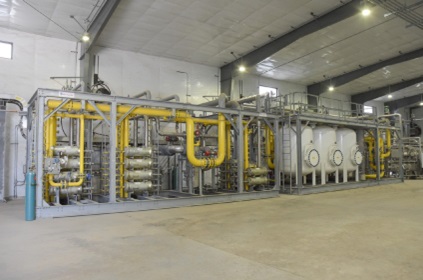
Carbon Dioxide Separation (Air Liquide)
Air Liquide uses polymeric membranes to remove carbon dioxide (CO2) from biogas produced in landfills. The membranes act as molecular sieves that separate the methane and CO2 in the biogas. The process can treat raw biogas flows ranging from 50–10,000 standard cubic feet per minute (SCFM). The resulting biomethane or RNG has a methane content of 95–99% and can be used as a substitute for natural gas.
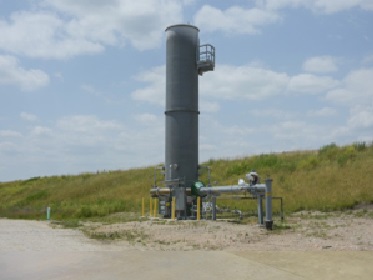
Thermal Oxidizer (John Zink Hamworthy Combustion Thermal Oxidizer)
As part of the purification process to transform biogas into RNG, some methane (CH4) is stripped out as “tail gas,” along with Carbon Dioxide (CO2) and other residual constituents such as Volatile Organic Carbon (VOCs), siloxanes, and Hydrogen Sulfide (H2S).
This tail gas is routed to the thermal oxidizer, and with the assistance of natural gas, is burned off and destroyed.
Nitrogen Pressurization (ARI Pressure Swing Adsorption [PSA] System)
This ARI PSA System is also known as the Nitrogen Removal Unit (NRU), which is used to separate nitrogen (N2) from the mixture of gases exiting the Air Liquide system. Five PSA vessels are filled with adsorbent carbon media. The media is specifically designed to capture methane (CH4) gas and release N2.
Each vessel undergoes a six-step cycle to adsorb and desorb CH4 and regenerate media for the next cycle. The 6 steps are: Feed, Rinse, Blowdown, Evacuation, Purge, and Pressurization. The five vessels operate in parallel through these six steps to provide continues operations. Gas flow between vessels is controlled by a valve skid, recycle compressor, and a vacuum compressor.
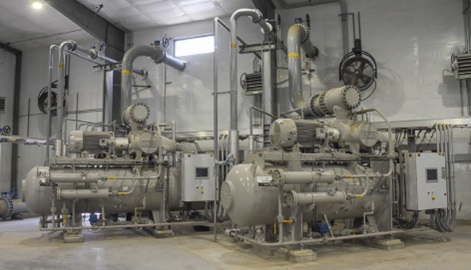
NRU Vacuum Compressor (Vilter VSG Single Screw Compressor)
The Nitrogen Removal Unit (NRU) Vacuum Compressor provides vacuum needed for the cycling processes of the ARI Pressure Swing Adsorption (PSA) system.
Associated piping networks circulate compressor oil to an oil cooler outside to release heat from the oil that is created during the compression process. The cooled oil is then returned to lubricate and cool the compressor.
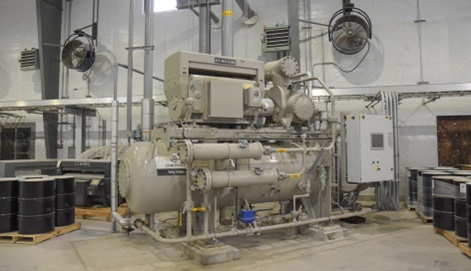
NRU Recycle Compressor (Vilter VSG Single Screw Compressor)
The NRU Recycle Compressor provides a vacuum needed to transport biogas from the Air Liquide carbon dioxide separation system to the ARI Pressure Swing Adsorption (PSA) system.
Associated piping networks circulate compressor oil to an oil cooler outside to release heat from the oil that is created during the compression process. The cooled oil is then returned to lubricate and cool the compressor.
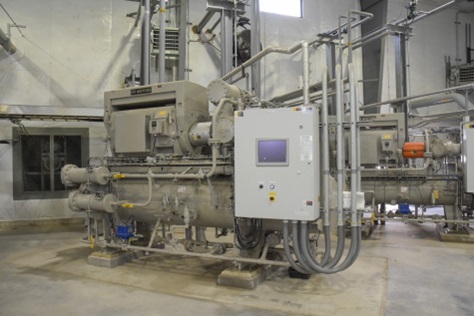
Stage 1 Product Compressor (Vilter VSG Single Screw Compressor)
Stage 1 compression is the first pressurization stage before final delivery of biogas into the pipeline. The compressor takes refined and upgraded biogas, now Renewable Natural Gas (RNG) from the ARI Pressure Swing Adsorption system and pressurizes it to 270 pounds per square inch (PSI).
Associated piping networks circulate compressor oil to an oil cooler outside to release heat from the oil that is created during the compression process. The cooled oil is then returned to lubricate and cool the compressor.
Stage 2 Product Compressor (Vilter VSG Single Screw Compressor)
Stage2compressionisthefinalpressurization stage before delivery of Renewable Natural Gas (RNG) into the pipeline. The compressor receives RNG from the stage 1 compressor and boosts the pressure to approximately 800 pounds per square inch (PSI). This pressure is necessary to transport the RNG through the delivery pipeline.
Associated piping networks circulate compressor oil to an oil cooler outside to release heat from the oil that is created during the compression process. The cooled oil is then returned to lubricate and cool the compressor.
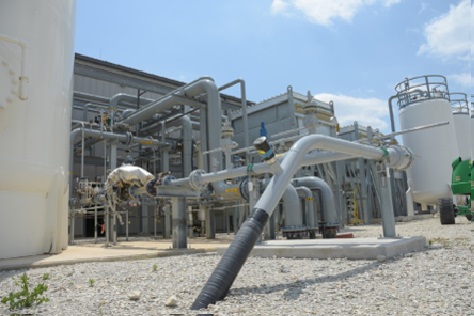
High BTU to Gas Pipeline
Will County constructed an approximately six mile pipeline to transport the RNG to the interconnect in Wilmington. The 4” coated carbon steel pipeline starts with a flange connection to the gas processing plant at the landfill, with an additional flange for a temporary launcher barrel connection. The interconnect point at the end of the pipeline has a flanged connection for a temporary receiver barrel and a flange to the gas operator’s facilities after which point the gas is no longer in the custody of Will County.
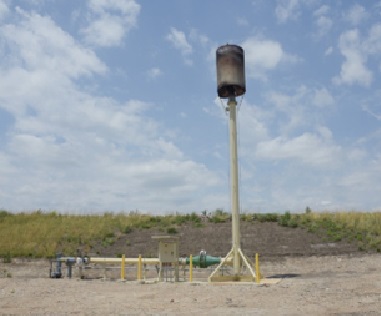
Off Spec Flare (Perennial Energy Flare)
Flaring is a necessary step in processing biogas, as it prevents the release of methane and other more harmful greenhouse gases into the atmosphere. Concentrations of different gases that compose the biogas may change over time as it exits the landfill and enters the facility requiring facility or process adjustments. While the facility or processes are adjusted to return the biogas to proper parameters, the biogas may become out of spec from the end user requirements. Therefore, the out of spec biogas has to be destroyed by the off-spec flare.
Condensate Collection
Condensate in a biogas processing facility primarily comes from the moisture present in the raw biogas. During the multiple stages of processing, the temperature of the biogas fluctuates. During these stages, the moisture is collected and pumped into onsite frac tanks. When the tank nears capacity, the condensate is pumped out into a tanker and shipped to a local wastewater facility for treatment.
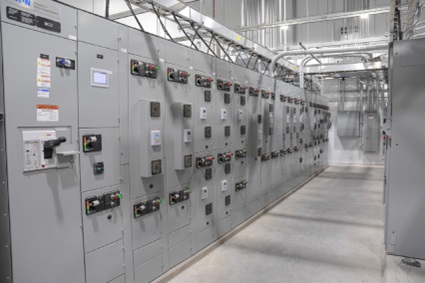
Electrical Room
The electrical room houses all relays, controls and switchgear for high voltage critical components. The area is constantly cooled to regulate temperatures of electrical components.